12 Ways to Troubleshoot CNC Router Bits
CNC router bits are essential tools in precision cutting, especially in industrial applications like furniture making and sign production. Proper care and technique can extend the life of these bits and ensure optimal performance. However, even the highest quality CNC bits, like those from Amana Tool®, can face issues without proper attention. In this guide, we’ll explore common problems and how to address them to keep your projects on track.
Benefits of Amana Tool® Precision CNC Tooling for Industrial Applications
Exceptional Precision and Quality: Amana Tool® CNC tooling is engineered to deliver high precision and superior cutting quality, ensuring accurate and consistent results for complex industrial applications.
Durability and Longevity: Manufactured using high-quality materials and advanced engineering processes, Amana Tool® CNC tooling offers enhanced durability and longer tool life, reducing the frequency of tool replacements and downtime.
Versatile and Comprehensive Range: Amana Tool® provides a wide variety of CNC tooling options tailored for different industrial needs, including CNC router bits, CNC insert router bits, solid carbide compression spiral bits, miterfold & signmaking bits, doormaking router bits, and many more.
Compared to less expensive bits, Amana Tool® CNC bits are made with precision-ground shanks and the finest carbide. This ensures a better grip in the collet, prevents slippage, and enhances the lifespan of the bit, making them an excellent investment for serious woodworkers and manufacturers.
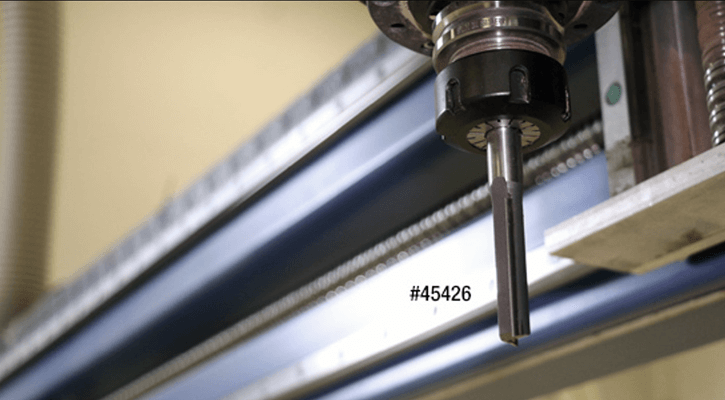
1. CNC Router Bit Wear and Tear
Issue: Gradual wear from continuous use reduces the cutting efficiency of CNC bits.
How to Avoid:
- Choose the right material for your router bit depending on the workpiece.
- Implement a proper maintenance schedule (cleaning, inspection, replacement when necessary).
- Hone bits regularly to maintain edge sharpness.
2. CNC Router Bits Dull Quickly
Issue: Rapid dulling can occur due to improper speed and feed settings or working with tough materials.
How to Avoid:
- Adjust the feed rate and spindle speed according to material hardness.
- Use carbide bits for harder materials to extend tool life.
- Avoid overheating through better speed control and adequate cooling.
3. CNC Router Bit Breakage
Issue: Sudden bit breakage often results from excessive force or incorrect bit type for the job.
How to Avoid:
- Match the bit size and type with the job and material.
- Use multiple passes for deeper cuts to reduce stress on the bit.
- Ensure the bit is properly secured and avoid applying too much pressure.
4. CNC Router Bits Overheating
Issue: Overheating can burn the bit and the material, leading to reduced cutting efficiency.
How to Avoid:
- Use proper cooling techniques, such as air or liquid cooling.
- Ensure the correct spindle speed to prevent heat build-up.
- Keep bits clean and free of material build-up to improve airflow.
5. CNC Router Bits Producing Poor Finish
Issue: Rough surfaces or poor finishing can be caused by dull bits or incorrect cutting parameters.
How to Avoid:
- Sharpen or replace dull bits.
- Adjust feed rate and spindle speed to match material properties.
- Reduce vibration by ensuring bit stability and using appropriate cutting techniques.
Pro Tip:
- Use a two-flute bit where fine finish is paramount. Two flutes balance the bit, eliminating vibration that degrades the cut finish. Two cuts per revolution yield a smooth surface, but feed rate is slightly reduced.
6. CNC Router Bits Vibration Problems
Issue: Vibration can cause poor cut quality and premature wear on both the bit and machine.
How to Avoid:
- Ensure the bit is tightly secured and balanced.
- Use shorter bits to reduce deflection during cutting.
- Adjust feed rates to minimize vibration.
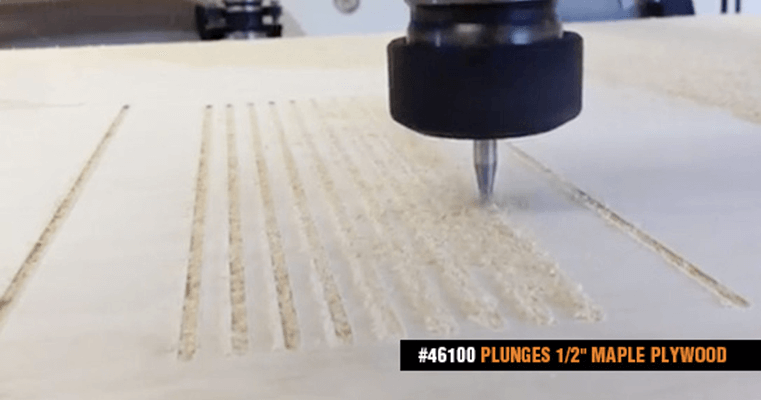
7. CNC Router Bits Material Build-up
Issue: Material build-up on the bit can cause friction, overheating, and affect the cutting performance.
How to Avoid:
- Regularly clean the bit during long jobs to prevent excessive build-up.
- Use the right cutting tool coating (such as titanium) to reduce material adhesion.
- Apply lubrication or misting systems to prevent material accumulation.
8. Improper Bit Size for the Job
Issue: Using a bit that’s too small or too large for the material or the detail required can lead to inefficiency and poor results.
How to Avoid:
- Select the appropriate bit size based on the specific job requirements, especially for detailed work.
- For intricate cuts, use smaller bits and ensure your machine has enough precision to handle them.
9. Collet Slippage
Issue: If the collet is not properly tightened or if it is worn out, the router bit can slip, leading to inaccurate cuts or damage to the workpiece.
How to Avoid:
- Regularly inspect and replace worn collets.
- Ensure the collet is properly tightened before starting the cut.
- Avoid over-tightening, as it can damage both the bit and the collet.
10. Incorrect Bit Insertion Depth
Issue: Inserting the bit too shallow or too deep in the collet can lead to unstable cuts or bit damage.
How to Avoid:
- Insert the bit to the recommended depth—typically leaving about 1/8” of the shank exposed.
- Avoid bottoming out the bit in the collet, as this can cause vibration and poor cutting performance.
11. Using the Wrong Bit Type for the Material
Issue: Different materials require different bit types. Using the wrong type can result in poor finishes, material damage, or rapid bit wear.
How to Avoid:
- Choose a bit type suited for the material (e.g., spiral bits for wood, specialized bits for acrylic or metals).
- Reference material-specific recommendations for CNC router bits to match bit type with the material.
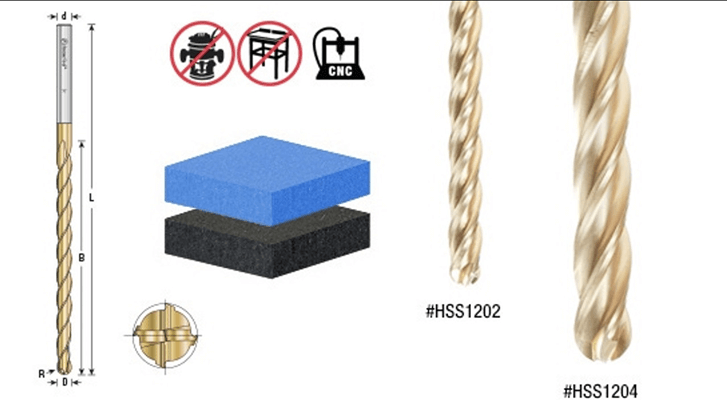
12. Incorrect Bit Flute Configuration
Issue: Flute configuration can dramatically affect cut quality and material removal. Incorrect configuration leads to chipping, poor finishes, or inefficient material removal.
How to Avoid:
- Select the right flute configuration (e.g., upcut, downcut, compression) depending on the material and desired finish.
- For clean edges on both sides of the material, compression bits are ideal; for fast material removal, upcut bits work well.
CNC router bit performance is crucial for precision work in industrial applications. Choosing the right bit, maintaining proper speed and feed rates, and practicing good maintenance habits can significantly reduce common issues like wear, dullness, overheating, and breakage. Investing in high-quality CNC bits, such as Amana Tool® products, ensures not only better performance but also a longer tool lifespan, helping you achieve excellent results consistently.