Meet Omer Deutsch: The Master Luthier Behind OD Guitars
In the world of fine woodworking and precision craftsmanship, few titles carry as much reverence as "master luthier." For Omer Deutsch, founder of OD Guitars, this distinction is well-earned. Based in Israel, Omer has spent the past decade blending his industrial design expertise with a lifelong passion for music to create stunning, custom electric guitars that are as much works of art as they are instruments.
We caught up with Omer following the NAMM 2025 show, where his creations were showcased at the prestigious Boutique Guitar Showcase. In this first installment of our *Profiles of Master Craftsmen* series, Omer shares his journey from industrial designer to renowned guitar maker, what inspires his work, and how he turns raw wood into tonal perfection.
Here’s what he had to say.
1. What drew you to building guitars?
I started playing guitar at 13, around the same time I got into building RC planes (which I still enjoy today). I wanted to combine these two hobbies, and with my experience as an industrial designer, I was able to take it to the next level and turn it into a business that I truly love.
2. Did you learn through formal study, apprenticeship, or self-teaching?
Both. I started learning whatever I could online, and at some point, I met a very experienced local luthier who wanted my help with design and CNC machining (which I had no previous experience with). So I started learning CNC work online and by trial and error, I managed to work my way up. We helped each other out; he taught me how to build guitars and I created designs and working files for his CNC.
Also, I have a degree in Industrial design which helped a lot with understanding design, practical methods and understanding customer's needs.
3. What’s your favorite part of the guitar-building process, and why?
Mainly carving shapes by hand, talking to customers and developing a relationship, but also improving my building process by planning tools, machinery and methods.
4. How do you select the wood for your guitars? Are there specific characteristics you look for?
I'm working with woods that I've personally tried in the past and I know it'll give me the best results in terms of sound capabilities that fit my target audience and their needs.
Furthermore, I tend to work with only air-dried and well-seasoned woods, so every time I encounter with an old stock that someone is trying to get rid of, I'll be the one to take it. I have a 20 years old ebony stash which is literally gold ;)
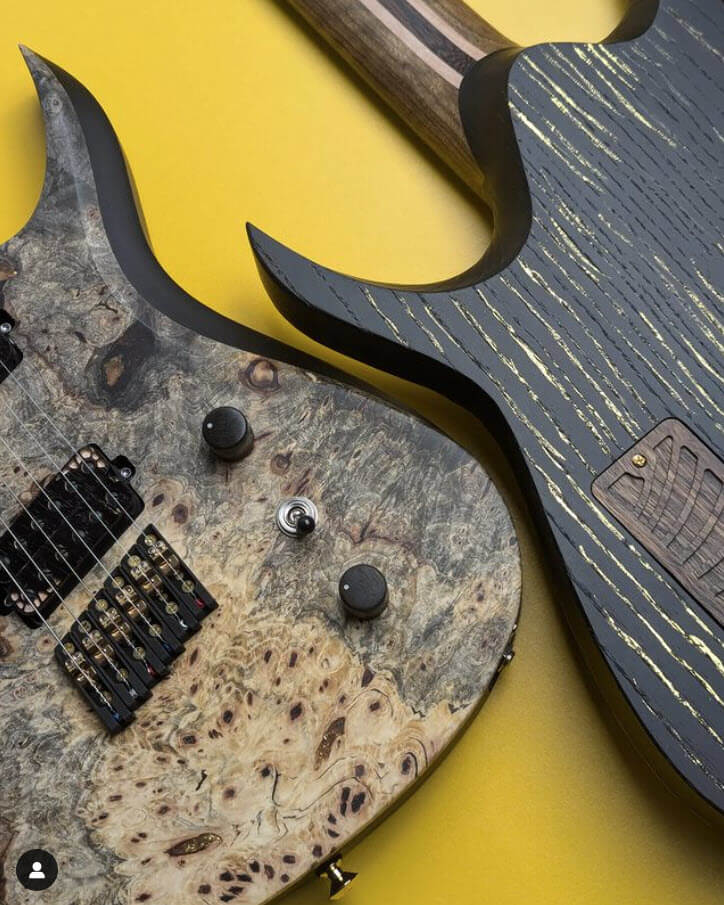
5. How does the type of wood affect the tone and playability of an electric guitar?
I see it as a chassis of a car, if you have a bad chassis and the best engine (pickups) the engine won't perform well, so this is why it's very important that the platform you are working with will be the best you can have, otherwise, you'll end up using expensive hardware for nothing.
The neck of the guitar is about 70% of the sound for me, it vibrates when plucking a string, if the neck is too stiff, the string will stop fast, if it's too soft, it will go out of phase, so there's a lot of Important things to consider when choosing the right woods.
6. Do you use CNC machines or mostly hand tools? How do you balance traditional craftsmanship with modern technology?
I use a lot of CNC machining, however, as opposed to what people have in mind, CNC is about 30% of the work load, the guitar won't come out from the machine ready to play, there's a lot of sanding, gluing, preparing the wood, adjusting, and more hand work.
Since I'm producing about 40 Custom guitars a year, I manged to develop a nice process for each stage that works best for me.
7. What’s your approach to customizing guitars for different players? Do you design around playing style, genre, or personal preference?
I start by talking with the customer about the type of music they like to listen to, play, and their favorite guitar to date.
Then I can start suggesting wood choices, pickups, scale length, etc.
8. What are some of the biggest challenges when building an electric guitar?
Definitely the neck build and the fret work, at the end of the day, if the neck is not comfortable to play, the player will end up hating it.
As for the fretwork, if the fretwork isn't good enough, the player will start having problems, buzzing strings and things no one wants to deal with other then a specialist tech guy.
9. Have you noticed any recent trends in guitar design or materials?
I did, using hard materials such as Aluminum in order to make the neck stable and problems-free, however for me as I explained before, I want to keep the neck vibrating and let it ring, work perfectly with the guitar and strings, even if it means you'll need to adjust the neck here and there.
Another trend I've noticed is developing all sorts of mechanisms, hardware that help the guitarist stay in tune so they won't have to adjust or worry about it at all.
10. Are there any innovative techniques or tools that have changed the way you build guitars?
YES, the main one is the Vacuum table on my CNC and the Amana RC-2255 2-1/2" fly cutter, I started using it and figured out a way to work everything without the need for a jointer or a thickness planner, it was a point in my life where I was able to ditch the planer/jointer and work everything on the CNC. Less noise, less dangerous and more accurate.
11. Where do you source your tools, and what do you look for in a supplier?
I get most of my cutting tools from ToolsToday. Their fast shipping—even to Israel—means I don’t have to wait weeks for a crucial bit to arrive. Plus, they stock the complete Amana Tool line, which is a big deal for me. I know that whatever I need, they have it, and I can trust the quality every time.
12. What’s your take on alternative materials like carbon fiber or composites in electric guitar construction?
I prefer the carbon fiber and composite materials on my RC gliders :) it's strong, lightweight and has about 5% advantage in a musical instrument, so I don't feel like it is necessary.
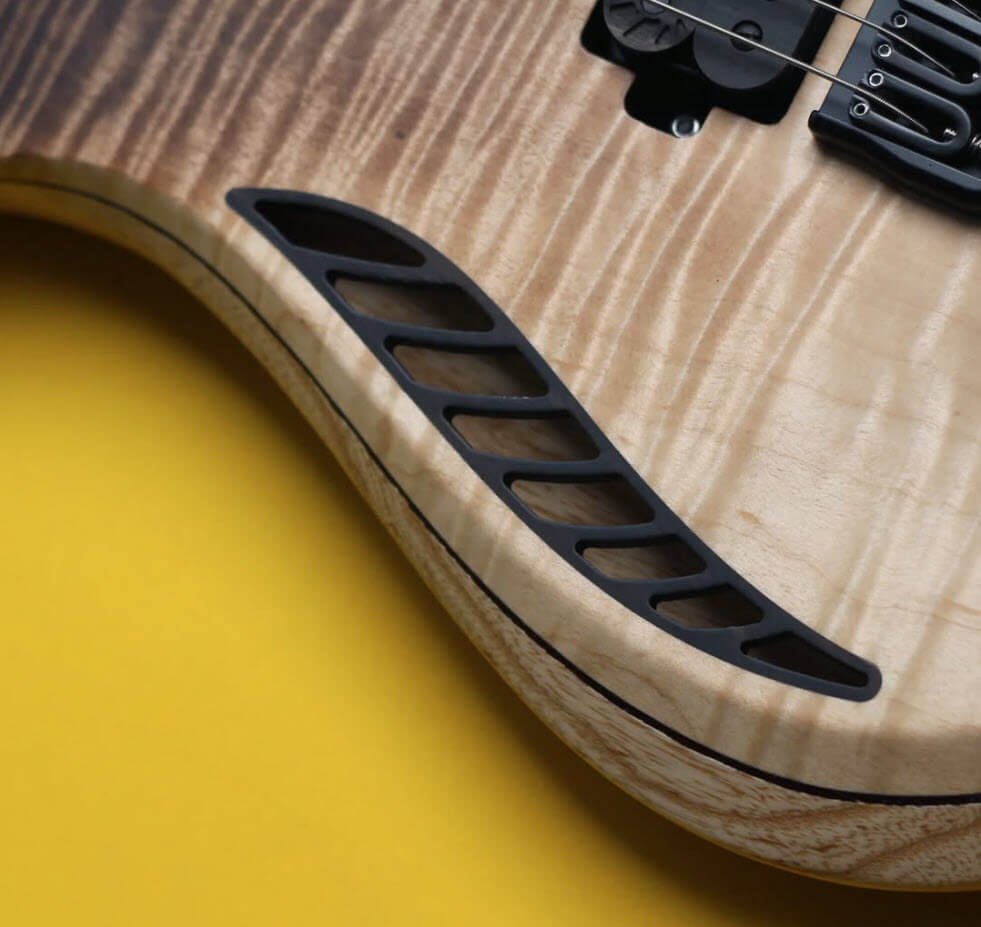
13. What advice do you have for guitarists looking to maintain their instrument for the long term?
- Clean after a long playing session, especially the fretboard.
- Keep the guitar in a well-seasoned environment as much as possible.
- Replace the strings whenever they are starting to rust, the pickup magnets will attract the rust.
- Don't store it in a bag, keep it in a place you can see it and play it whenever you feel like it! Otherwise, there's no point in having a guitar , it should be played, and looked at.
14. Are there any common mistakes players make that can damage a guitar over time?
- Not replacing the strings in time.
- Trying to flip it over the head in a show, ending up having it crash on the floor.
15. Do you have a favorite guitar you’ve built? What makes it special?
Probably the 2024 NAMM art piece I presented at the Boutique Guitar Showcase.
It was something I never tried before, using AI to develop an idea based on my prompt, and making it a reality even though it was just a 2d image.
There was a lot of hand work and CNC machining to create what I envisioned.
16. If you could build a custom guitar for any musician (living or dead), who would it be and why?
- Adam Jones from Tool
- Joe Satriani
- I discovered a band back in 2016 when they just started to get known and I wanted to build their guitarist an instrument, I've reached out to him and built him three guitars in total.
This player is Roman of Jinjer which is now one of the biggest heavy metal bands in the world.
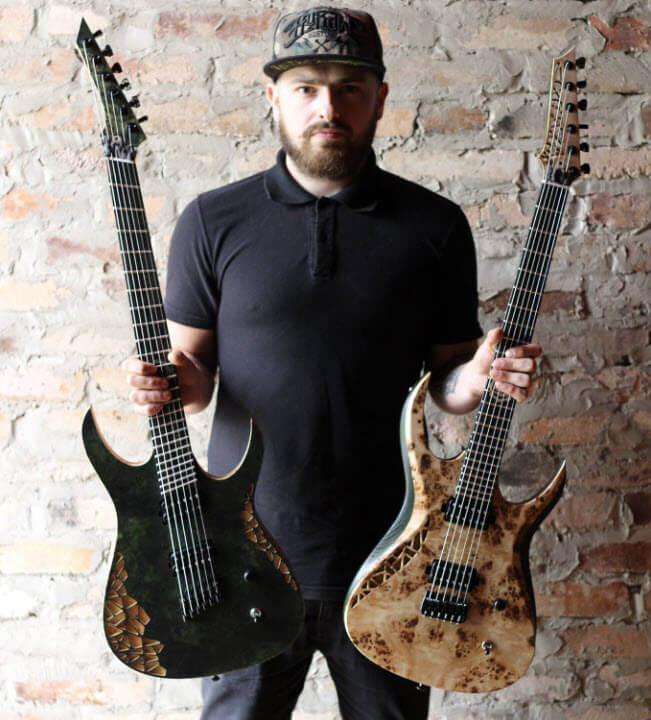
17. What advice would you give to someone looking to become a luthier?
Don't put all of your effort into being the best guitar builder, you'll need to know how to run a business and market yourself, most builders put all their eggs in the building methods, but if no one realizes they exist, it won't make any business.